Factors for Choosing Workblanks of Valves
Valves have wide usage. Nevertheless, valves play a great role in industries. For example, in power plants, valves can be used to control operation of boilers and turbines. In petroleum and chemical industry, valves are also used to control operation of the whole production equipments and technological processes. Workblanks commonly used for machining include casting, forging, proximate matters and weld assemblies. Categories, accuracy, roughness and hardness have direct impact on machining processes. The following factors should be taken into consideration when choosing workblanks of valves.
1. Requirements for materials of parts, tissues and performances of materials
Materials of parts stipulated on design drawings decide categories of workblanks. For example, parts made from forged steel must be forged into workblank by using forging. In terms of steel parts, when choosing workblanks, requirements on mechanical property of materials should be considered. Parts used for manufacturing high pressure valves generally choose forgings or castings so that materials have good mechanical property.
2. Structural shape and dimension of parts
Structure of parts is an important factor influencing workblanks choosing. Body having complicated structure can choose castings. Body having large dimension can choose sand mould forgings while body having small dimension chooses fired mould forgings.
3. Size of production program
The larger production program of parts is, the better economic effects are when adopting workblanks which have high accuracy and efficiency for manufacturing.
4. Conditions for manufacturing workblanks
Workblanks are chosen according local equipments and technological levels. Considering development, more advanced manufacturing methods should be adopted gradually.
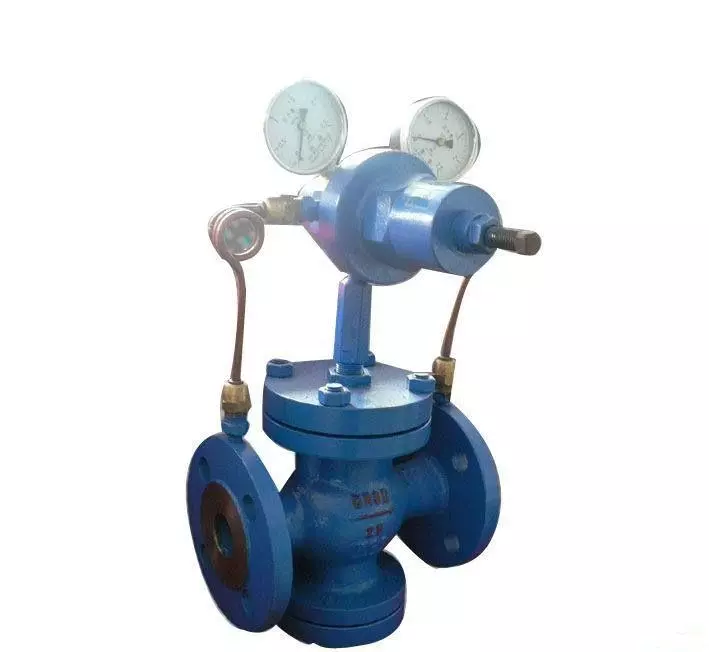